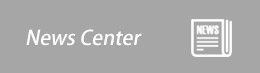
- A discussi...2025/4/18
- Spring Ren...2025/4/18
- The nation...2025/3/7
- Industrial...2025/3/7
- 2025 China...2025/2/14
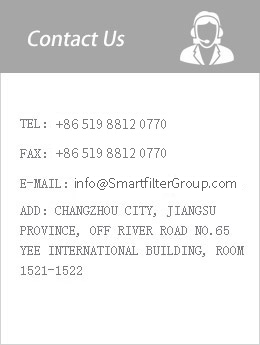
In late spring and early summer (April to May), industrial workshops are confronted with two major challenges: the risk of filter cloth mold caused by high humidity and heavy rainfall, and the accelerated aging of filter cloth due to high-temperature environments. As a core consumable in the chemical fiber industry, the maintenance of filter cloth directly affects production efficiency and cost. This article, in light of seasonal pain points, presents a scientific maintenance plan to help enterprises extend the lifespan of filter cloths and reduce downtime!
I. Mold and Moisture Prevention during the Rainy Season: Safeguarding the "Breathing Capacity" of Filter Cloth
The cleaning strategy has been upgraded
Cleaning frequency: During the rainy season, dust is prone to caking. It is recommended to shorten the cleaning cycle to two-thirds of the regular duration to prevent dirt from absorbing moisture and caking.
Cleaning method: It is recommended to combine ultrasonic waves with neutral cleaning agents, which can penetrate deep into the fibers to remove dirt and at the same time avoid the corrosion of chemical fiber materials by alkaline solvents.
Drying technique: After washing, use a low-temperature dryer (<60℃) or air dry in a well-ventilated area. Avoid direct sunlight to prevent the fibers from becoming brittle.
2. Storage optimization plan
Moisture-proof warehouse: Equipped with temperature and humidity monitoring devices, the humidity should be controlled at ≤60%. When storing, the filter cloth should be laid flat or hung vertically to avoid folding and indentation.
Isolate the source of mold: New filter cloth and old filter cloth should be stored separately. Before using the old cloth, a mold inhibitor should be sprayed on it.
Ii. High-temperature Warning: Selection and Maintenance of Heat-Resistant Filter Cloth
Summer Filter Cloth Selection Guide
High-temperature resistant material
PTFE filter cloth: With a temperature resistance of up to 260℃, it is suitable for filtering high-temperature tail gas in the chemical industry.
Nylon filter cloth: Resistant to instantaneous high temperatures.
Air permeability optimization: Select twill or monofilament woven structures to reduce pore blockage caused by high-temperature expansion.
2. High-temperature operation specifications
Temperature monitoring: Install a surface temperature sensor for the filter cloth. The polyester filter cloth should be ≤90℃. When the temperature exceeds the limit, activate the spray cooling system.
Anti-sticking coating: It is recommended to use Teflon-coated filter cloth to reduce the difficulty of cake removal caused by material adhesion at high temperatures.
Iii. Seasonal Inspection and Emergency Response
1. Daily checklist
Surface condition: Observe whether there are mold spots, hardening or local discoloration (signs of high-temperature burns).
Sealing test: During the rainy season, focus on inspecting the sealing strips at the edge of the filter cloth to prevent moisture from seeping in and causing bypass leakage.
2. Emergency repair plan
Minor damage: Use fiber thread of the same material and high-temperature resistant adhesive for on-site repair.
Large-scale tearing: Replace immediately and trace the cause (such as misaligned filter plates or sharp impurities), and the old cloth can be returned to the factory for regeneration.
Changzhou Xiahua Environmental Protection Technology Co., Ltd. specializes in the production and operation of industrial filtration materials for many years, mainly in the chemical industry, and the products are exported to many countries. Xiahua mainly produces the filter cloth, filter bag, pressure filter bag, etc., Xiahua filter cloth, use heart!